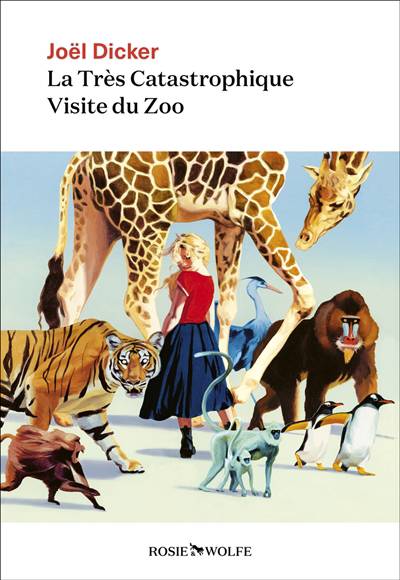
Every industry has its own indices, metrics, measures, and KPIs they use on maintenance. The main reason why we measure these indices is to determine if our maintenance organization is moving forward in the right direction. However, some indices may not be as simple as we think.
There is a wide selection of measurements and indicators for the maintenance function. We can measure the number of breakdowns, downtime, availability, mean time indicators, lubrication costs, set-up time, repair time, maintenance costs, MRO spare parts costs, and so on. For plants implementing TPM, the primary measure of their performance will be OEE or Overall Equipment Effectiveness. It is also difficult to provide a benchmark on what industry standard is for MTBF, cost, and so on because, again, industries are diversified. Having a consistent MTBF of 700 hours in a month for manufacturing will be more than satisfactory, but not for a power plant or distribution industry. This means that if we have an MTBF of 700 for all distribution poles, then the 20 hours means that the city is experiencing a black-out as there are 720 days in a month. This book is not just about knowing the formulas, and equations to use but having a deeper understanding of what we include and exclude in them. Some of these includes:
- What formula are we using on Availability, especially when calculating OEE?
- If a shipment was returned to the plant because of defects, is the Quality Rate adjusted on the date the product was manufactured?
- If the machine is not loaded and sitting Idle, is the No-Load included as a Planned Downtime?
- Is maintenance in agreement with this that no load is a Planned Downtime?
- Is set-up and changeover a Planned or Unplanned downtime?
- Have we separated on what to include and exclude as Planned and Unplanned downtime?
- Have we agreed on what we shall consider a breakdown and not a breakdown?
- Is everyone clear on the definition of breakdown and what do we include as breakdown or not especially in calculating MTBF, and MTTR where the denominator is the frequency of failures and breakdown.
- For manufacturing industries who suffered minor stoppages in their equipment, are these losses clearly separated from the breakdown especially when the downtime is prolonged due to no available technician.
There are many interesting topics I have written that should provide the reader some clarification on t Selecting the Right KPI's for Maintenance
- Which Formula Should We Use on Availability?
- Why having an OEE of 85% is Not Always World-Class
- Clarity On When Do We Declare a Breakdown or Failure?
- Confusion Between Breakdowns and Minor Stoppages
- Where Can We Use MTBF?
- Limitations of MTBF
- A Deeper Meaning of Reliability
- Why MTTR and RCFA are the Opposite of Both Worlds?
- Mean Time to Set-up Explained
- Mean Time between Assists (MTBA) Explained
- The Most Important Measure for the Storeroom racy
- Other MRO Storeroom and Spare Parts KPIs
- Tracking Small things Matter Most
- Maintenance is as Strong as its Weakest Link
- Achieving World Class Maintenance Level Can Now Be Measured
- Improving the Breakdown Rate and MTBF
- Who Should Monitor the Overall Equipment Effectiveness
- Frequently Asked Questions on Maintenance Indices
- Tips on Maintenance Indices
- Treat Maintenance as a Business
- People are the Key In Improving These Maintenance Indices
- The Challenges of Today's Maintenance in This Global Pandemic
- The Difficulty in Standardizing These Measurements
- The Integrity of Our Maintenance Indices These common Maintenance Indices
Nous publions uniquement les avis qui respectent les conditions requises. Consultez nos conditions pour les avis.