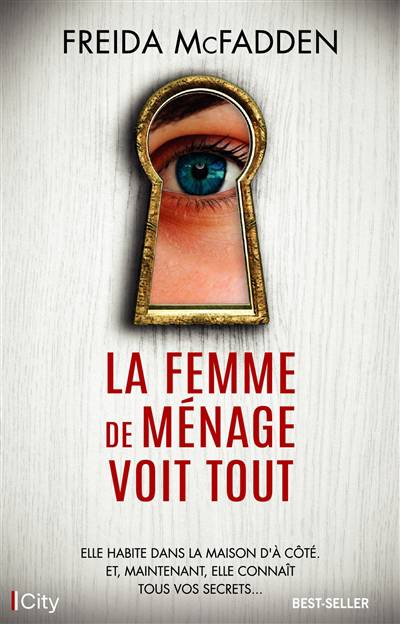
The lean operational concepts and techniques help make things more efficient for patients by reducing waste and wait times. This focuses on getting employees involved, constantly getting better, and thinking about what the customers want. All workers in the company, including doctors, staff, and support staff, always try to find ways to save time and money and get rid of anything that doesn't help patients, using lean methods in healthcare.
To ensure that the production team members on the assembly line always have everything they need, Toyota has organized all the necessary systems and support staff. If you go to one of their factories where things are put together, you can see this with your own eyes. Even though patients are more important, some people say that Toyota spends more money on training and supporting its employees than hospitals do. Toyota helps its team members focus on their duties and the truck in front of them, which leads to better results and overall satisfaction.
Nous publions uniquement les avis qui respectent les conditions requises. Consultez nos conditions pour les avis.