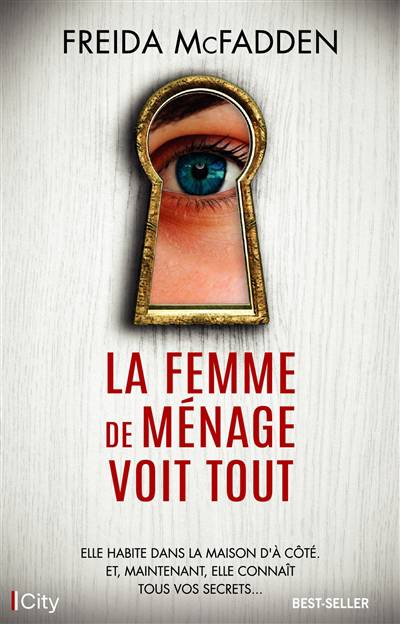
Giving machines and operators the power to notice when something is wrong and quickly pause their work. This helps companies to increase quality at every step of the process and to have workers and machines work separately for better efficiency. Jidoka is a fundamental concept in the Toyota Production System, which is an important way of doing things in Toyota factories. It is one of the two main principles, along with just-in-time.
Jidoka is a system that helps identify problems quickly because if a problem happens, work immediately stops. This helps make things better and prevents mistakes by fixing the main reasons for problems.
Jidoka is sometimes referred to as autonomation, which means using automation along with human intelligence. This is because it allows machines to determine if parts are good or bad on their own, without needing someone to watch them. This means that operators don't have to constantly watch machines. This helps them to be more productive because one operator can control many machines at once. This is called multiprocess handling.
The idea of jidoka started in the early 1900s when Sakichi Toyoda, who started the Toyota Group, made a machine that would stop on its own if a thread broke in a textile loom. In the past, when a thread would break on the loom, it would make a lot of bad fabric. So, someone had to watch each machine. Toyoda's invention allows one person to operate multiple machines. In Japanese, jidoka means automation, but it is a word created by Toyota that has additional meanings of being more humanistic and creating value.
Nous publions uniquement les avis qui respectent les conditions requises. Consultez nos conditions pour les avis.